|
|
Home Made Boards (6188 Posts)
|
Topic |
Home Made Boards |
|
On 5/15/2004
Frank
wrote in from
(24.170.nnn.nnn)
Has anyone tried using the roarockit with a vacuum pump? If so how'd it turn out, and how complex was it to set up and use?
|
|
|
|
|
On 5/14/2004
stanley w
wrote in from
(209.6.nnn.nnn)
Does anyone know technique for making your own decks that have spoon shapes or kicktails and kickfronts?
|
|
|
|
|
On 5/14/2004
Alex Maier
wrote in from
(142.173.nnn.nnn)
For my woodwork class final project i'm building a speed board drop thru set up, I was thinking a board like the landyachtz drop thru race, and I was wondering, Does anyone have the dimensions of the cut out for the trucks? also, how hard is it to add some concave to the board? how compicated of a jigg/press does this require? cause i would like to have concave, but im wondering if its worth the extra work.
Thanks
|
|
|
|
|
On 5/14/2004
Frank
wrote in from
(24.153.nnn.nnn)
David, looks real good. I like the look of that maple. Its an even better feeling when it rides.
Congrats
|
|
|
|
|
On 5/14/2004 Duane
wrote in from
(68.15.nnn.nnn)
Maybe lapping crude cup-and-cone looseballs makes sense, but not high quality precision bearings. I wouldn't bother running in bearings unless the competition was fierce, and had a very strong downhill element. One place this (will) be true is skatecar racing, the aero drag is reduced by 80% so friction of wheels and bearings becomes much more important, If the race goes down I'll be prepped to the nines, including run-in bearings. And my secret sauce for increasing the speed of urethane... Ahhh, a race where physical talent matters not, that's my kind of race.
|
|
|
|
|
On 5/14/2004 george g.
wrote in from
(159.87.nnn.nnn)
David-good job, the shape reminds me of an early version of a Comet Cross "fat ass" which never really made production, they thinned the tail a touch. The broadleaf maple is beautiful and strong too. good luck!
|
|
|
|
|
On 5/14/2004
david
wrote in from
(192.211.nnn.nnn)
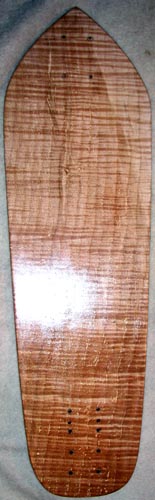
heres my little slalom board project. the board is made from solid broadleaf maple. about 29" long by 9.5 wide with a 20" inner hole wheelbase. its a sweet little ride, i already cruised it before i put the coats of wood finish on it. i'm still going to wax the whole thing then do some nice grip job on it. plus its the first board i ever made myself. stoked!!!
|
|
|
|
|
On 5/13/2004
george g.
wrote in from
(162.42.nnn.nnn)
Wow, interesting about Hut's bearings. If I would have know that I would have asked him at the worlds 03! He is still a guy us just over 40 yrs can aspire to, he still kicks ass!
Lapping compound in bearings? Hugh? anybody? in my thoughts the tolerances are pretty tight. I don't see how the lap could be consistent. It isn't like a rifle barrel or heads/valves. Those are a few of the things I have lapped. The compound would have to be pressed in and rotated to polish the already polished surface. How about Extrude honing for bearings?
I like the idea of building a homemade bearing break in thing, that kinda makes sense.
|
|
|
|
|
On 5/13/2004
silversurfer
wrote in from
(24.62.nnn.nnn)
Have you guys checked out Hugh's Home Made bearing conditioning machine?
Check it out here:
http://www.hugh308.homestead.com/bearingwars2_condition.html
|
|
|
|
|
On 5/13/2004
FL
wrote in from
(65.119.nnn.nnn)
When I was putting on DH races at Laguna Seca in the late 70's ,John Hutson {remember him ?} let slip that he had this old coot machinist run his bearings in for him . Said it took quite awhile , but the results were worth it . As I recall , he was consistently on the podium . He referred to the process as "brinneling" [sp.?] and it made the bearings run quite a bit smoother and faster . Some years later, BMX'ers used a fine lapping compound in their hubs for a similar result.Lapping compound is an a abrasive and must be thoroughly cleaned from the bearings .FL
|
|
|
|
|
On 5/13/2004 ooops
wrote in from
(207.69.nnn.nnn)
radius= Circ.
|
|
|
|
|
On 5/13/2004
hugh r
wrote in from
(24.48.nnn.nnn)
I see where my mistake is... I didn't convert inches to feet during my calcs... I have to fix my page!
So when I reclac... it looks like a 101 mm wheel spinning at 300 rpm would cover 3.54 miles in one hour... I guess for my numbers to work I'll need a wheel around 10' tall!
Thanks Dave! And yes... I am a dope... HR
|
|
|
|
|
On 5/13/2004 DAve G
wrote in from
(207.69.nnn.nnn)
P.S, If you want a job land surveying...Don't call me, I'll call you!!!;-) I can't afford that much time in court explaining why that lil' ole lady's Farm in Kentucky actually belongs to my client in eastern West "by God" Virginia!! ;-)
|
|
|
|
|
On 5/13/2004 Dave G
wrote in from
(207.69.nnn.nnn)
Hugh, I gotta go..but 300 rpm =18,000 rph. A 101 has close to a 1' radius so it would be closer to 18,000' /5280 = 3.4 mph I did these #'s in my head while brushing my teeth..but NO WHERE NEAR what you got! Off to the river.
|
|
|
|
|
On 5/12/2004 hugh r
wrote in from
(69.166.nnn.nnn)
Hey Math guys! Can one of you please verify my math and let me know if I screwed up??
I figure that the following wheels spinning at 300 RPM would acheive the following speeds:
101 mm - 42.61 mph 83 mm - 34.89 mph 70 mm - 29.43 mph
Thanks a lot! HR
|
|
|
|
|
On 5/12/2004 Duane
wrote in from
(68.15.nnn.nnn)
Forgot to mention, product numbers with a "T" in them refer to tracer, it is the thread of yellow weave that is used for automated lay-up systems (it is barium loaded so it shows up on x-rays, the quality control on a wing, for instance, is to x-ray through many layers and digitally compare the pattern of tracer threads to the standard, pretty clever). Tracer is said to disapper when wetted, it does not ! Avoid it if you care about appearance.
|
|
|
|
|
On 5/12/2004 Duane
wrote in from
(68.15.nnn.nnn)
Weaves: plain weave is rather plain-looking, and doesn't take contours well. that doesn't matter much for skateboards. 2x2 Twill, instead of each "thread" going over then under, goes over two then under two. This makes each strand a bit more straight, so tensile loads up a bit faster (it doesn't have to straighten out as many kinks first). 2x2 also gives that classic look with a diagonal pattern. The harness satins cross over more threads, a 5HS will cross over 5 fill threads before weaving under, 8HS 8 threads. These take contours extremely well, in fact 5HS can cover a baseball without kinking. For our use I would think the 2x2 twill gives the best balance. The harness satins tend to unravel more easily when cut. These are all 0/90 degree fabrics, with equal weight in both directions. The other useful material is unidirectional, with cabon in one direction, and only a thin glass knit scrim in the other to hold things in place. Available in 12" widths, this is good stuff to add 0 degree stiffness, or even 30 or 45 degree "non-twist" reinforcement at the nose and tail. As for weights, I find the 5.7 oz (per square yard, or sometimes square meter) to be awful light, you have to use too many layers. The 6K tows usualy come in at 10-11.5oz/yd this is perfect for skates, often one layer will be enough. 12k tow is too heavy for skates. Note that the 6k tow 2x2 twill is about the same price as 3k twill, so you get twice the weight at the same price. To figure out the true added weight, assume you'll be lucky to get 50% fiber loading (for this you must use vaccum), so easily double the weight of the cloth will be added, more for sloppy jobs. They key with fiber is to wet it correctly, I like low viscosity epoxy, or better yet vinyl ester, it soaks in real easy. The #1 problem with first tries with carbon is not wetting the cloth, you can't see like with glass cuz the damn stuff is black ! Another tip is to use brand new scissors, and tape all edges before cutting, then cut the tape in half. You will not be able to remove fray from the cloth when wetting with resin, it frays into 1,000 strands and mars the project.
|
|
|
|
|
On 5/12/2004 Paul
wrote in from
(65.213.nnn.nnn)
Duane, So which weave is the best for boards? Or what are the advantages of one over the another? Plain Weave, Harness Satin, Twill,Unidirectional, or Double Bias?
Thanks.
|
|
|
|
|
On 5/11/2004 Duane
wrote in from
(165.121.nnn.nnn)
ran into this joint for carbon and glass, best prices I've seen, better than the 'bay
http://www.discountcomposite.com/inven.html
I'm going to give them a try
|
|
|
|
|
On 5/11/2004 Duane
wrote in from
(68.15.nnn.nnn)
To stop delaminating (wood), water down some Titebond II glue slightly, to thin it, and apply to the delam spot. if you have access to air, use some to blow the glue in, otherwise just apply way too much and give it time to soak in., helping it with a small brush or blade if you have one. Put on some wax paper, some wood blocks, and clamp securely (but not too tight) for 30 minutes, then release and wipe off the mess with a damp cloth. Don't soak it when wiping down, you can sand off any excess mess later. If it is glass, you'll need to use some epoxy, the 2-part kind in the glue section works fine, and follow the same instructions above, except clamp less tightly, and clean off excess with something gnarly like laquer thinner (only on the edge, it will bite the surface)
|
|
|
|
|
On 5/11/2004 Scott S.
wrote in from
(142.177.nnn.nnn)
I was just wondering if anyone has any tips to stop a board from delaminating?
Please help me, I was to save my board!
Thanks, Scott
|
|
|
|
|
On 5/11/2004 psYch0Lloyd
wrote in from
(198.160.nnn.nnn)
joseph: for custom pivot bushings, you may want to contact Steve in AZ. i know that he and some other people around here have been making pivot bushings for all kinds of trucks.
and i believe that duane's right about that idea of sj ryan's... it does seem totally doable. don't know the costs of such a contraption but a trip to the dump or secondhand shops should fetch something around $25 bucks, should you want to motorize the whole thing you could add the cost of our little motor +10% s/h and you should have a grand total of $25. maybe you might want to try your hand at making the test rig from scratch... i can almost see it now, it would look something like a big belt sander.
|
|
|
|
|
On 5/11/2004
Brady
wrote in from
(65.80.nnn.nnn)
I like Duane`s idea of using a shaft for loading and spinning for break-in. How about a shaft, or bolt, 8mm OD, and have 8 bearings set up with spacers and preloaded with a torque wrench. You can then get a peice of pvc pipe that will slip pver the bearings. Maybe add strips of lead to it. Duct tape it snugly, then place in drill. You can then run the drill at a set rpm and time it for so long. Maybe even put the drill in a vice and turn it it all directions>> vertically up, vertically down, horisontal, and maybe 45% up, and 45% down.
This should give you a pretty much controlled environment that all types of bearings can be broke in with all types of loads.
maybe??
|
|
|
|
|
On 5/11/2004 hugh r
wrote in from
(69.166.nnn.nnn)
Now on the tread mill... suppose a fishing scale was attached to each deck so that you could read the pounds of pull... would THAT be a meaningful measurement of rolling resistance?
I could picture noting the weight on the scale at the beginning of the test... then at the end... then comparing all the data.
Thoughts?
I don't have a tread mill laying around, but I just may have to try and pick up a cheapie at a thrift store... how much should an older non-electronic go for? HR
|
|
|
|
|
On 5/11/2004 Duane
wrote in from
(68.15.nnn.nnn)
All this spouting about break-in devices for bearings, and SJ Ryan's idea on the Vendor's forum about strapping skateboards to a treadmill, makes far more sense. You could mount several boards at once, and it is a pretty real-life simulation.
|
|
|
|
|